(ILI) Inspection Systems
Tooling Capabilities:
RestoLine’s patented delivery method targets unpiggable pipelines ranging in ⌀’s (200 mm – 1.5 m) with lengths up to 600 m from a single entry point. The robotic tooling is configured with NDE Sensors that relay real-time information, allowing for rapid assessment of the internal pipeline condition; Tooling configured with multiple sensors eliminate multi-pass inspections, allowing for complete assessment and data collection in one single pass.
Laser Profiling
All of the measurement data is transferred from the on-board centralizer PC to the control unit. This data is used to calculate the inner profile of the pipe, measure section loss, and create a graphic display for review at the control unit.
Laser Measurement
Inspection systems for pipes >150 mm include a laser measurement sensor to identify internal defects & corrosion. With the laser displacement sensor, it is possible to measure internal defects with micron accuracy at long distances.
High Res PTZ Camera
The centralizer’s inspection head provides high definition video feed. The head has pan and tilt functions and an integrated color camera. With the high quality resolution, 8x optical zoom, manual and automatic focusing.
Ultrasonic Inspection
The ultrasonic inspection head has rotating sensor probes. It can measure both the pipe wall and lining thickness with an accuracy of .18 mm. The signals are converted by the on-board PC in the electronics module.
Inspection Sensors Capability and Benefits:
Crack Inspection for Unpigabble Lines:
Facility piping is generally not designed with piggability as a requirement. Many unpiggable conditions exist with navigability that requires 1D back to back bends, mitered and dual diameter inspection capabilities that are not possible with conventional ILI methods (pigging). RestoLine’s tethered (ILI) system can navigate these complex geometries and require no launching facility in order to insert the tooling.
Pump Stations
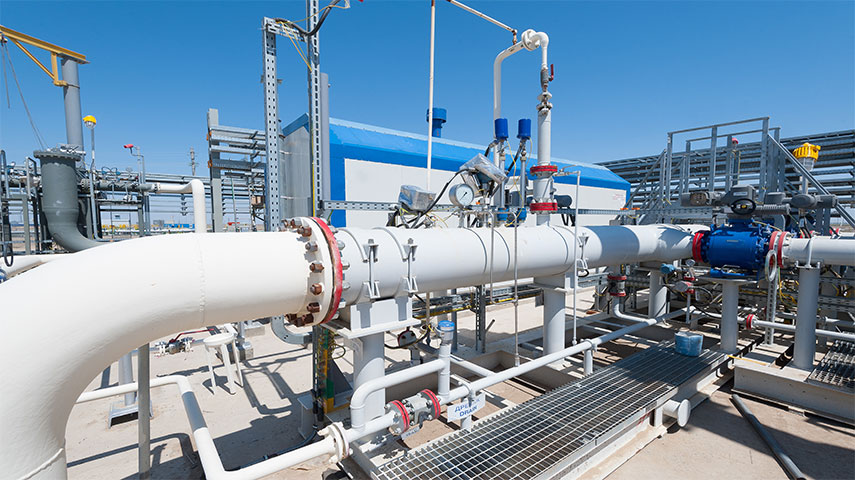
Pump Stations that connect mainline to and from the pipe units are often above ground but have buried portions. These piping sections range in size with diameter inconsistencies and a large amount of bends dependent upon the layout design.
Compressor Stations
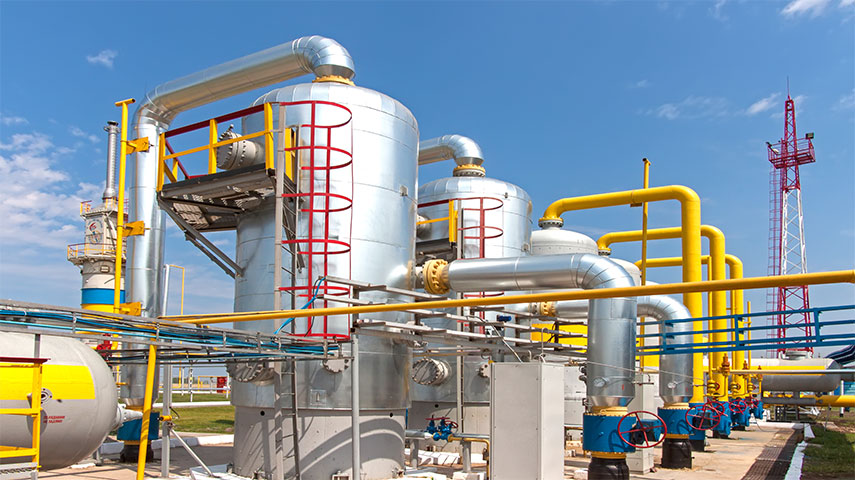
Compressor stations have piping that connects the mainline to the compressors. But generally there is inline equipment such as scrubbers placed before the compressor and after the coolers. These also range in diameter with a large number of bends.
Tank Farms
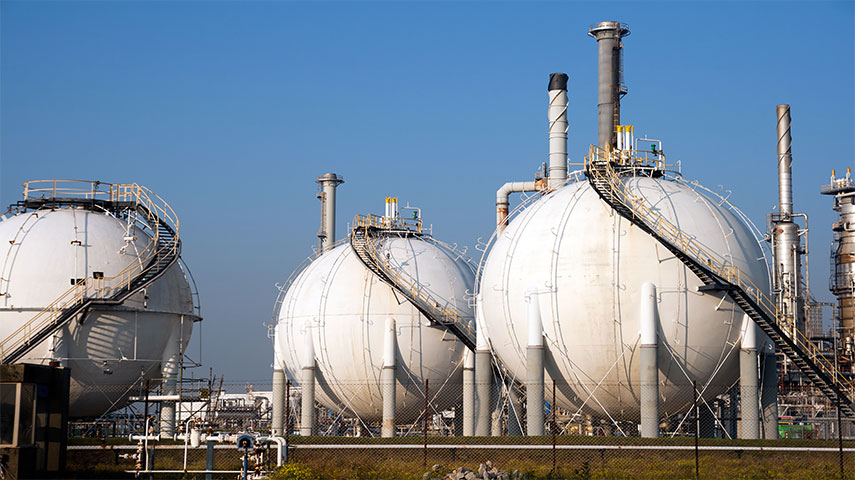
Tank Farms have interconnected pipe that is normally above ground with longer lengths than stations. The diameter of the piping will normally vary but typically will be similar to the mainline diameters and closely match the process flow rates.